Precision parts processing produces parts from materials and processes, which are very precise processes. The workpiece processing requirements in precision machining generally require precision machining of parts in the form of numerical control. Its specific accuracy is reflected in the following 4 points:
Dimensional accuracy
The degree of conformity between the actual size of the processed part and the centre of the tolerance zone of the part size.
Shape accuracy
The degree to which the actual geometry of the machined part surface conforms to the ideal geometry.
Position accuracy
The actual positional accuracy difference between the relevant surfaces of the part after machining.
Interrelationships
Usually, when designing machine parts and specifying the machining accuracy of parts, attention should be paid to controlling the shape error within the position tolerance, and the position error should be smaller than the dimensional tolerance. That is to say, for precision parts or important surfaces of parts, the shape accuracy requirements should be higher than the position accuracy requirements, and the position accuracy requirements should be higher than the dimensional accuracy requirements.
The processing flow of high-precision machining parts
Review the project and select the appropriate processing technology
During your free manufacturing consultation, our engineer experts will review your project; the process will be discussed with you. We will gain an in-depth understanding of your part and its application and collect the data we need to select the appropriate machining process and materials. We may ask the following questions:
- What temperature will the part be exposed to?
- What force will the part be subjected to?
- Will the part be exposed to liquids or gases?
- What is the role of the parts?
. After you confirm the order, we will formulate a suitable machining plan for CNC machining of precision parts for your parts, analyze the drawings of the parts to be machined, process the parts and adopt appropriate machining techniques for the machining content of the parts.
CNC precision machining mainly includes precision turning, precision milling, precision grinding and other processes. Usually, these processes are combined in the processing of a part:
- Precision turning: Most of the precision light alloy (aluminum or magnesium alloy, etc.) parts in the aircraft are processed by this method. Generally, a natural single crystal diamond tool is used, and the radius of the blade arc is less than 0.1 microns; when processed on a high-precision lathe, an accuracy of 1 micron and a surface unevenness with an average height difference of fewer than 0.2 microns can be obtained, and the coordinate accuracy can reach ±2 microns.
- Precision milling: used for processing aluminum or beryllium alloy structural parts with complex shapes. Relying on the precision of the machine tool’s guides and spindles to obtain high mutual positional accuracy, high-speed milling with carefully ground diamond tips can achieve precise mirror surfaces.
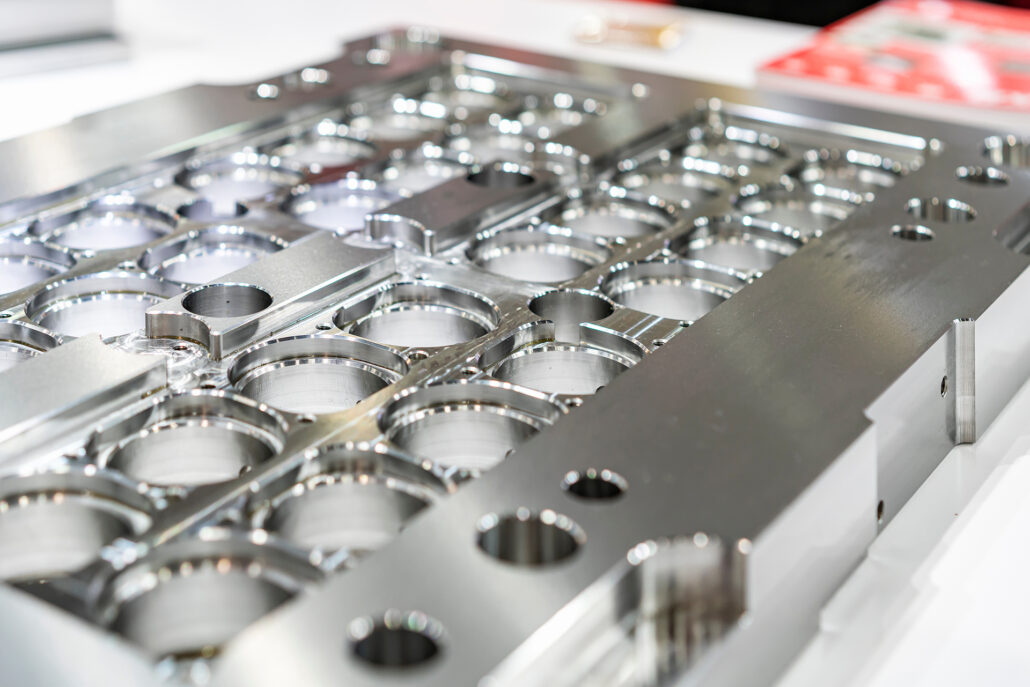
Choose the right material
On some occasions, the higher the hardness of the material, the better, but this is not absolute. We should consider the application scenarios and functions of the parts and select the appropriate materials. The commonly used materials are the following 5 types:
. Aluminum:
Aluminum is probably the most widely used CNC milling material. Machining faster than other materials makes aluminum a more useful material for CNC machining. Due to its lightweight, non-magnetic properties, corrosion resistance and low price, aluminum is widely used to produce aircraft parts, auto parts, bicycle frames and food containers.
Stainless steel:
Stainless steel alloys are immune to most stains and rust. Favoured for its strength and corrosion resistance, the material can be used in surgical equipment to electronic hardware. Stainless steel is a very versatile material that is relatively light and durable, expanding its use in various industries.
Carbon steel:
Carbon steel is also one of the popular materials to consider for CNC machining. It is available in various formulations to choose from based on your application requirements. The material is mainly used in CNC machining due to its durability, safety, long shelf life, and economical and environmentally friendly properties.
Brass:
Widely regarded as one of the simplest and most cost-effective materials for precision machining services, brass is chosen to create complex parts that require complex functions. Brass is easy to machine, smooth has a clean surface, and can be used to manufacture medical devices, consumer products, electronic hardware and contacts, accessories, commercial products, and more.
Titanium:
Titanium is heat and corrosion-resistant, making it a viable option for many industrial applications. T titanium is widely used to make medical implants, aircraft parts, and jewellery, unaffected by salt and water.
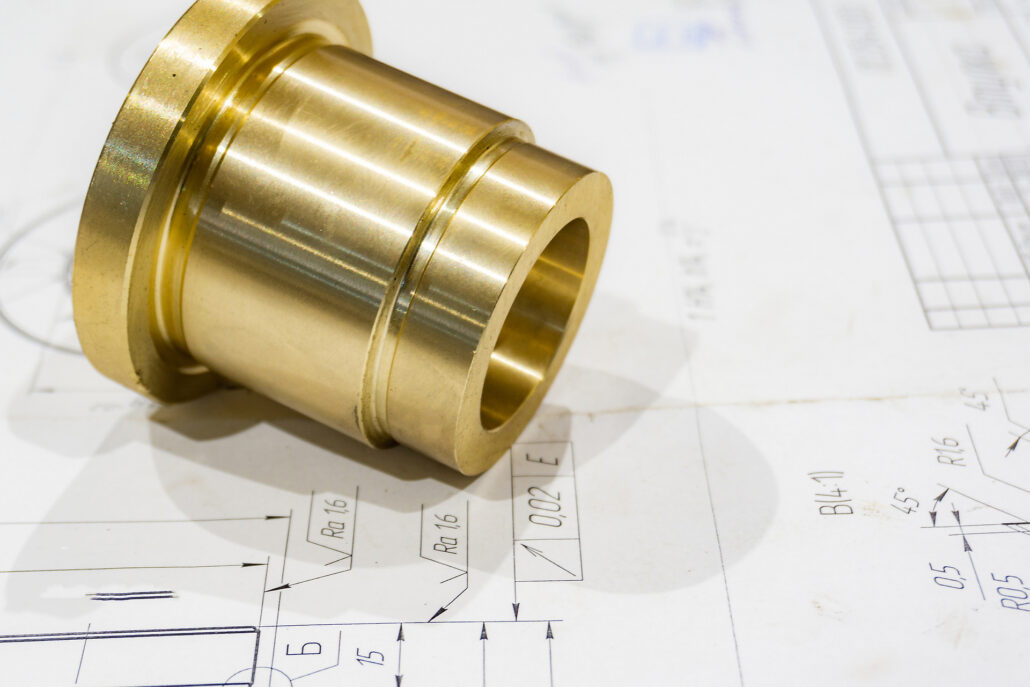
Manufacturing parts
The most important part of high-precision parts processing is the writing and design of the process flow because the program steps of part processing, the selection of benchmarks, the selection of processing tools, the selection and installation of fixtures, the determination of processing strategies and process parameters will affect the quality of the product.
Quality inspection
We pay attention to the full inspection of product quality during the processing of high-precision parts. Only qualified products can be shipped. If they do not conform to the drawings, secondary processing will be performed to meet the requirements of the drawings, such as size, accuracy, tolerances, and technical parameters.
In the quality inspection, Keyanng uses a three-coordinate measuring instrument, which refers to an instrument that can express measurement capabilities such as geometric shape, length and circumference indexing within the spatial range of a hexahedron. The measuring functions of the CMM include dimensional accuracy, positioning accuracy, geometric accuracy and contour accuracy, etc. It is the best instrument for measuring whether precision parts are qualified.
Keyanng’s Precision Machining Services
If you are looking for a reliable supplier for your precision parts, Keyanng will never let you down! Submit a free manufacturing consultation request, and we will provide you with a quote and support within 12 hours.